The Environmental Benefits of Using Precast Concrete
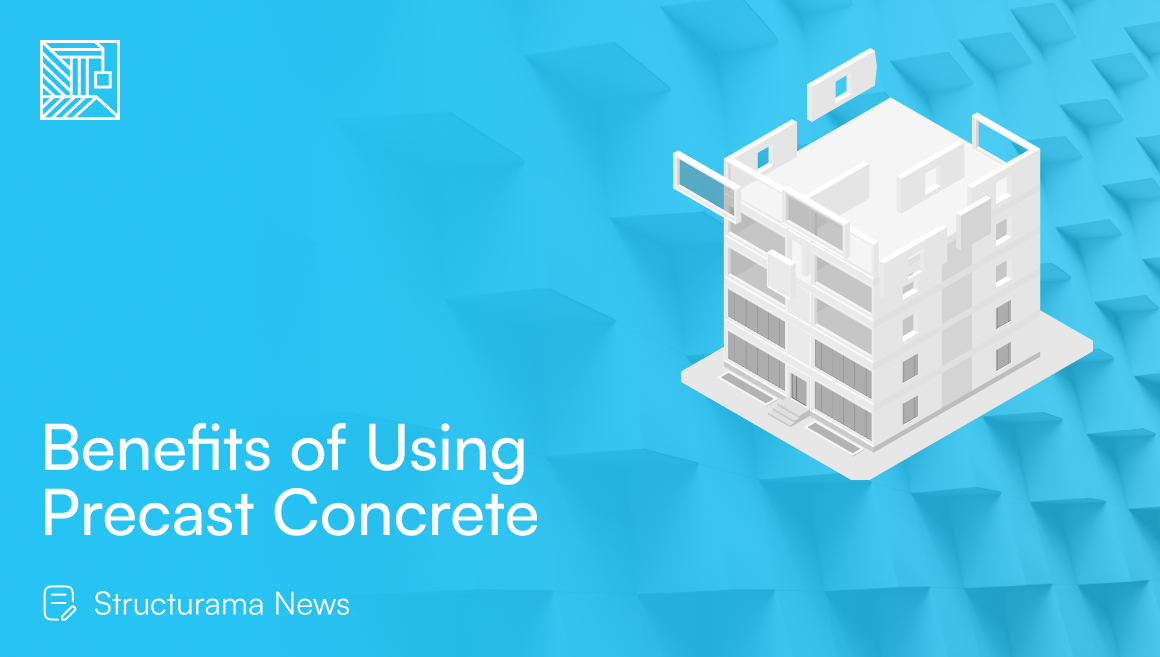
Although it was always desirable to have the environment in mind when it comes to any of our daily practices, now is the time we’re all as a society coming to realize that it’s no longer a choice. We are now seeing the consequences of the irresponsible choices of the past, when maybe no one knew better, or no one cared enough to do better, or couldn’t afford to do better.
Now is the time for environmental awareness and solutions that are both cost-effective and eco-friendly, and in the construction world, precast concrete is precisely that. This blog will explore precast concrete’s various advantages and potential disadvantages, including its role in reducing carbon footprints, promoting sustainability, and offering greater control over design, production processes, transportation, and installation.
What Is Precast Concrete?
To truly understand and appreciate all of the environmental advantages of using precast concrete in construction, one must first know how it differs from traditional, conventional concrete.
While conventional concrete is a construction material that is poured and cured at the location of the construction process, precast concrete is manufactured in a completely controlled environment of a factory setting. It is cast in a reusable mold, and once it reaches the desired strength, while critical factors like humidity and temperature are regulated, it is transported to the construction site and lifted into place.
Depending on the prefabricated system chosen, this approach can significantly reduce on-site completion activities, enhancing sustainability and ensuring a higher quality of details and joints that might otherwise be less precise if done on-site.
This fact alone implies its more optimized energy usage and reduced emissions, since extensive on-site operations of traditional construction methods more often than not involve high greenhouse gas emissions and energy consumption. We’ll discuss more on that below.
What Are the Environmental Benefits of Precast Concrete?
Innovative construction materials of the present aim for sustainability, which stands for meeting the present needs without compromising those of the future, i.e. leaving the future generations with a possibility of a quality life on a planet with finite resources. There are several ways through which precast concrete achieves sustainability standards.
1. Reducing CO2
First and foremost, we want to once again highlight the reduction of carbon emissions in construction by using precast concrete. As mentioned above, precise control over the manufacturing conditions of precast concrete results in decreased energy consumption. In addition, the use of high-performance raw materials or those with the ability to be recycled further contributes to reducing CO2 emissions by minimizing the demand for new resources and extending the lifecycle of precast elements.
Moreover, the transportation carbon footprint is reduced by the fact that the final product is transported to the construction site, unlike traditional raw materials that require extensive on-site mixing. This approach not only decreases emissions related to transportation but also cuts down on the CO2 typically emitted during on-site processing and preparation. This reduction is further supported by off-site production in controlled factory settings, which optimizes resource recovery and raw material efficiency.
In addition, the longevity and durability of precast concrete structures reduce the need for frequent reconstructions, repairs, and replacements, which are more common with traditional building materials. Specifically, precast panels used as the exterior infill of buildings offer a dual benefit: they provide a high-quality facade while also protecting the insulating materials beneath from daily wear and weather-related degradation. This dual-layer protection results in lower maintenance needs over time, enhancing overall resource efficiency and minimizing material waste.
2. Improving Air Quality
Precast concrete, being produced in a controlled environment with precise measurements and strict quality control, includes the use of eco-friendly additives and admixtures. These additives reduce the emission of harmful pollutants (such as volatile organic compounds) and contribute to enhanced air quality, leading to healthier indoor and outdoor environments.
3. Recycling of Waste Materials
Precast concrete manufacturers are committed to sustainability by recycling leftover materials. Whether it’s concrete, steel, or even water, much of the waste is repurposed. Water plays a significant role in concrete production and surface treatment processes, and recent practices have focused on optimizing water usage due to its status as an increasingly valuable resource. By implementing water recycling measures, manufacturers reduce consumption and further minimize the environmental impact.
In terms of steel, major efficiency gains are achieved through the use of advanced technological machines designed for the production of reinforcing steel, which optimizes usage and reduces waste. In regions where access to such technology is limited, the adoption of BIM (Building Information Modeling) design provides significant value. BIM helps optimize the raw materials used by improving design accuracy and reducing unnecessary surplus. Together, these practices foster a circular economy, ensuring that fewer raw materials are consumed and that environmental degradation is minimized.
4. Energy Conservation and Thermal Efficiency
Precast concrete’s thermal mass plays a crucial role in energy conservation. It can absorb heat during the day and release it slowly at night, reducing the need for additional heating and cooling. When combined with proper insulation, precast concrete structures offer significant long-term energy savings, helping to lower the overall carbon footprint of a building by reducing its reliance on energy-consuming HVAC systems.
In addition, the management of critical details plays a decisive role in optimizing energy performance. Since prefabricated components are treated and controlled in a factory setting, issues like thermal bridges or acoustic problems that often arise during on-site construction are minimized. However, it is important to note that the management of certain joints varies based on the prefabricated system chosen. This variation affects the way components are manufactured and assembled, emphasizing the need for precise control to ensure consistent thermal and acoustic efficiency.
5. Long-Term Durability and Material Efficiency
One of the most significant environmental advantages of precast concrete certainly lies in its above-mentioned exceptional durability and efficient use of materials. Precast structures are designed to last for decades, ensuring they remain resilient against environmental factors and reducing the strain on natural resources. By optimizing the design, precast components require fewer raw materials, meaning less is harvested from the environment, and there’s minimal waste at the end of their lifecycle.
This long-term approach to construction not only addresses present-day sustainability concerns but also ensures that we are building with future generations in mind. Precast concrete offers a solution that balances immediate needs with the broader goal of creating sustainable, eco-friendly infrastructure that stands the test of time.
What Are the Environmental Benefits of Using the Precast Graphic Concrete Walls?
Precast graphic concrete walls combine aesthetic appeal with sustainability in a unique way. The artistic textures and designs minimize the need for additional finishes, leading to savings in both materials and labor. By opting for precast graphic concrete walls, builders not only achieve striking architectural designs but also reinforce their commitment to sustainable practices.
Reduction of Waste and Lower Consumption of Materials for Higher Performance
While energy efficiency and reduced carbon footprint are key environmental benefits of precast concrete, its contribution to minimizing waste and optimizing material usage deserves special mention. The highly controlled factory production process ensures precise material allocation, effectively reducing waste and preventing overproduction.
Furthermore, the inherent durability of precast concrete reduces the need for frequent repairs or replacements, which not only saves on materials but also contributes to a more sustainable building lifecycle. By minimizing both initial material consumption and ongoing maintenance needs, precast concrete supports more efficient, long-term construction practices.
Precast Also Means a Healthier Work Environment and Safety for Employees
The factory-controlled production of precast concrete offers significant benefits not only for the environment but also for worker safety and health. Unlike traditional construction sites, where exposure to dust, noise, and other hazards is common, precast factories operate under strict controls for air quality, noise levels, and safety protocols.
Workers benefit from reduced dust generation, enhanced ventilation, and access to personal protective equipment like respirators, ensuring their long-term health and safety. Additionally, this controlled environment contributes to consistently high-quality finished products. By manufacturing precast components under optimal conditions, factors such as precision, durability, and overall performance are better managed, leading to superior results compared to conventional methods. This dual focus on human welfare and product quality demonstrates the precast industry’s commitment to responsible and efficient building practices.
Are There Any Disadvantages to Precast Concrete?
While there are a few challenges associated with precast concrete, these are generally minor when weighed against its numerous advantages. The initial investment in molds and specialized equipment can be higher, and transporting large precast elements may pose logistical issues. Additionally, the design flexibility may be slightly limited compared to on-site construction, and modifications on-site can be more complex.
However, these challenges are often overshadowed by the time and cost savings, durability, and sustainability that precast concrete provides. Once in place, its low maintenance, reduced environmental impact, and long-term efficiency make these minor hurdles worth navigating. For most projects, the long-term benefits far outweigh any initial concerns, making precast concrete a smart, future-forward choice.
Paving the Way for Sustainable Construction
As the construction industry continues to evolve, the need for sustainable building solutions has never been more urgent. Precast concrete stands out as a green alternative that meets the demands of both environmental responsibility and modern efficiency. Its ability to reduce carbon emissions, minimize waste, and optimize material usage makes it a key player in the movement toward more eco-friendly construction practices.
By choosing precast design services, we are not only addressing the immediate environmental concerns but also investing in a long-term solution that promotes sustainability for future generations. As we look ahead, it’s clear that precast concrete offers a viable path toward building a greener, more resilient future.